Objective
It shall be the policy of the University of Tennessee to maintain exposure to airborne hazards below applicable permissible exposure limits (PELs) while on the job. A respirator is one means to provide protection when other controls are not available or are ineffective.
The primary objective is to prevent harmful exposure to airborne contaminants. Where feasible, this shall be accomplished through engineering controls (e.g. substitution of less toxic materials, enclosure or isolation, or general or local exhaust ventilation). When effective engineering controls and/or administrative controls are not feasible, or while they are being instituted or evaluated, the use of appropriate respiratory protection will be required.
Scope
This program shall apply to all respirators used by UTHSC employees and students for the purposes of health protection. The program shall not apply to respirators used for comfort or to prevent exposure to nuisance levels of air contaminants. The Respiratory Protection program is maintained by Campus Safety, Research Safety and Occupational Health (Student and Employee) Contract personnel have a responsibility to have a qualified respiratory protection program in place prior to any work that requires these controls.
This policy shall be used as guidance to refine departmental or local policy and guidelines. Because workplaces differ substantially, each program must be tailored to the specific conditions of the workplace. The program must consist of worksite-specific procedures governing the selection, use, and care of respirators. The program must be updated as often as necessary to reflect changes in workplace conditions and respirator use.
Implementation of the provisions within this policy is the responsibility of each UTHSC department under the advisement of Campus Safety, Occupational Health, the Infection Prevention and Control Program and Research Safety. Participation in the Program is at no charge to UTHSC employees and students. Expenses associated with respirator equipment will be covered by individual departments.
Infectious Disease Control Plans and Polices are reserved for provisions specifically applicable to the prevention of occupational exposures to airborne pathogens in the Research, Clinical and Educational sites, for which the use of respirators is appropriate. Each unit is responsible for determining applicability to specific employees or disease entities.
Abbreviations, Acronyms and Definitions:
- Air-purifying Respirator – a type of respirator with an air-purifying filter, cartridge, or canister that removes specific air contaminants by passing ambient air through the air purifying element.
- Assigned Protection Factor (APF): the OSHA assigned work- place level of respiratory protection that a respirator or class of respirators is expected to provide to employees when the employer implements a continuing, effective respiratory protection program.
- Atmosphere-supplying Respirator– a respirator that supplies the respirator user with breathing air from a source independent of the ambient atmosphere, and includes supplied air respirators (SARs) and self-contained breathing apparatus (SCBA) units.
- Canister or Cartridge – a container with a filter, sorbent, or catalyst, or combination of these items, which removes specific contaminants from the air as it passes through the container.
- Employee Exposure – exposure to a concentration of an airborne contaminant that would occur if the employee were not using respiratory protection.
- Filter– a component used in respirators to remove solid or liquid aerosols from the inspired air
- Fit Test – a protocol to quantitatively or qualitatively evaluate the fit of a tight-fitting respirator on an individual.
- Half-mask respirator: Respirators that cover the mouth and nose, including N95 and elastomeric cartridge equipped respirators.
- Immediately dangerous to life or health (IDLH) – an atmosphere that poses an immediate threat to life, would cause irreversible adverse health effects, or would impair an individual’s ability to escape from a dangerous atmosphere.
- Loose Fitting Face piece – a respiratory inlet covering that is designed to form a partial seal with the face or head
- NIOSH approval – the approval of a respirator for worker protection by the National Institute for Occupational Safety and Health (NIOSH).
- Powered Air Purifying Respirator (PAPR) – an air purifying respirator that uses a blower to force ambient air through air-purifying elements to the inlet covering.
- Respiratory Inlet Covering – that portion of a respirator that forms the protective barrier between the user’s respiratory tract and an air-purifying device or breathing air source, or both.
- SDS – Safety Data Sheets – Documentation providing safety information for hazardous materials that is compliant with the OSHA Globally Harmonized System (GHS) and meets the current regulatory requirements for these documents. Replaces material safety data sheets (MSDS).
- Self-Contained Breathing Apparatus (SCBA) – an atmosphere-supplying respirator for which the breathing air source is designed to be carried by the user.
- Supplied Air Respirator (SAR) or Airline Respirator – an atmosphere-supplying respirator for which the source of breathing air is not designed to be carried by the user, but it taken from a remote location.
- Tight-fitting Face piece – a respiratory inlet covering that forms a complete seal with the face.
- TOSHA – Tennessee Occupational Safety and Health Administration.
Procedure
Voluntary Respirator Use
Employees may choose to voluntarily use respirators, even though use is not required. When employees voluntarily use a respirator they shall perform the following:
- Receive a medical evaluation before first use of the respirator
- Clean, store, and maintain the respirator in accordance with the provisions of this plan.
Supervisors shall give employees, who voluntarily use a respirator, a copy of the information contained within the Appendix A: Voluntary Use of Respirators.
Medical Evaluations:
- The Occupational Health Department shall coordinate medical evaluations for respirator users. The initial medical evaluation includes a medical questionnaire to be completed by the affected employee. Prior to using a respirator, employees shall request for a respirator medical clearance, complete the Respirator Medical Evaluation Questionnaire and submit it to the Occupational Health Department for review. Based on information provided in the medical questionnaire, the nurse or physician may perform medical tests, consultations, or diagnostic procedures to make a final determination regarding the employee’s ability to use a respirator.
Employees have the opportunity to discuss the questionnaire and examination results with the Occupational Health nurse or physician.
- The Occupational Health Department shall maintain a copy of the authorization in the employee’s medical record. All examinations and questionnaires shall remain confidential between the employee and the Occupational Health Department.
- After an employee has received clearance to use a respirator, additional medical evaluations shall be provided under the following circumstances:
- The employee reports signs and/or symptoms related to their ability to use a respirator, such as shortness of breath, dizziness, chest pains, or wheezing.
- The Occupational Health Department or supervisor determines that another evaluation is necessary.
- Information from this program, including observations made during fit testing and program evaluation, indicates a need for reevaluation.
- A change occurs in workplace conditions that may result in an increased physiological burden on the employee.
- The employee has a change in health status.
Respirator Selection
The basic purpose of any respirator is to protect the user from specific inhalation hazards. Respirators provide protection by removing contaminants from the air before inhalation or by supplying an independent source of respirable air.
Campus Safety, Research Safety shall evaluate with the applicable supervisor or Principle Investigator the following information for each work situation or task:
- The nature of the hazard;
- The physical and chemical properties of the air contaminant;
- Warning properties of the hazardous chemical;
- The adverse health effects of the respiratory hazard;
- The relevant hazardous exposure level;
- The results of workplace sampling of airborne concentrations of contaminants;
- The nature of the work operation or process;
- The period of time respiratory protection will be worn by employees during the work shift;
- The work activities of the employees and the potential stress of these work conditions on employees wearing the respirators;
- Fit test results; and,
- The physical characteristics, functional capabilities, and limitations of the various types of respirators.
Appropriate respirators shall be selected from among those approved and certified by the National Institute for Occupational Safety and Health (NIOSH) and the provisions of 29 CFR 1910.134 (Respiratory protection in General Industry) or 29 CFR 1926.103 (Respiratory Protection in Construction) as appropriate.
Supplied-Air-Respirators (SAR) and Powered Air Purifying Respirators (PAPR) that are used on campus: Users of these hoods are exempt from the fit-testing provisions of this policy, however medical evaluations and training must occur.
Fitting of Respirators
Fit testing must occur prior to initial use of the respirator and annually thereafter. Fit test procedures will follow those prescribed by OSHA in appendix A of the Respiratory Protection Standard (29 CFR 1910.134). The employee shall be refitted when observations are noted regarding an employee’ condition which could affect respirator fit. Conditions to look for include facial deformities or scarring, cosmetic surgery, significant dental work or an obvious change in body weight. Employees are responsible to report any such conditions and to request repeat fit testing. Employees shall be given the opportunity to repeat fit testing at any time to ensure their comfort and protection.
- Qualitative fit testing: Half-mask respirators, including N95s will be fit tested by UTHSC personnel using an OSHA-approved qualitative fit testing procedure.
- Quantitative fit testing: Tight-fitting facepiece respirators with an Assigned Protection Factor greater than 10 (i.e. full-facepiece, SCBA, SAR) will be fit tested by UTHSC personnel using an OSHA-approved quantitative fit testing procedure.
- PAPRs: No fit test is required; however, a medical evaluation and clearance is required.
General Respirator Use
Respirators are to be worn by employees when required for a given task or by the work area.
Respirators that depend on a tight facepiece-to-face seal for effective performance, including disposable N95 respirators, are not to be worn by employees with conditions that prevent acceptable fits. Examples of these conditions include facial hair that interferes with the facepiece seal absence of normally worn dentures, significant facial deformities or scars, temple pieces of glasses or headgear that projects under the facepiece seal.
If an employee must wear corrective glasses or goggles while wearing respiratory protection, the supervising department shall ensure that they are worn in such a manner that they do not interfere with the seal of the facepiece to the face of the wearer.
The supervising department shall determine the types and numbers of employee positions that are required to use respirators and ensure adequate compliance to accomplish work.
The supervising department shall permit employees to leave the respirator use area to wash their faces and respirator facepieces as necessary to prevent skin irritation associated with respirator use.
The supervising department shall permit employees to leave the respirator use area to change the filter elements or replace air-purifying respirators whenever they detect the warning properties of the contaminant, chemical vapor breakthrough, or they detect a change in breathing resistance or as otherwise required.
The supervising department shall ensure that storage and inspection procedures are identified and followed. When respirators are cleaned, they shall also be inspected during cleaning.
The supervising department shall ensure that respirators are immediately repaired, or discarded and replaced when they are no longer in proper original working condition.
The supervising department shall ensure that employees perform a User Seal Check upon donning the respirator and prior to entering the work area for all respirators on which such a test is possible to be performed.
A pre-use operational check (fit, battery condition, and flow rate) must be performed prior to every use of a PAPR. The user is responsible for this.
Evaluation of Program Effectiveness
- Frequent unscheduled observation of activities throughout the facility will be conducted to confirm proper respirator use. This may be included as part of the periodic Campus Safety, Research Safety, and Occupational Health building inspection program.
- Observations and discussion with respirator users throughout the campus will be conducted to evaluate compliance.
- The overall effectiveness of the respirator program will be evaluated as necessary by the program administrator with actions taken to correct any defects found in the program.
Use of Respirators within Immediately-Dangerous-to-Life-or-Health Atmospheres
Where an oxygen deficient atmosphere (less than 19.5% by volume) or an IDLH atmosphere exists, UTHSC employees will not be allowed entry to work unless specifically trained and certified for such entries.
Employees, who enter immediately dangerous to life or health (IDLH) atmospheres under non- emergency escape conditions, shall use a pressure demand supplied air respirator with auxiliary self-contained air supply or a pressure demand self-contained breathing apparatus.
When entering IDLH atmospheres, employees shall perform the following procedures:
- At least one employee shall be located outside the IDLH atmosphere while entry occurs.
- Communication shall be maintained between the employee in the IDLH atmosphere and the employee(s) outside the IDLH atmosphere.
- The employee(s) outside the IDLH atmosphere shall be trained to provide effective
- emergency rescue.
- The employee(s) outside the IDLH atmosphere shall be equipped with (1) a pressure demand supplied air respirator with auxiliary self-contained air supply or a pressure demand self-contained breathing apparatus, and (2) appropriate rescue retrieval equipment.
Tuberculosis Respiratory Protection:
The certification of air-purifying respirators under 42 CFR Part 84, Respiratory Protective Devices, will enable respirator users to select from a broader range of certified respirators.
All of these new respirators will meet the performance criteria recommended by CDC for respiratory devices used in health-care settings for protection against Mycobacterium tuberculosis (Mtb), the infectious agent that causes tuberculosis (TB). The CDC published “Guidelines for Preventing the Transmission of Mycobacterium tuberculosis in Health-Care Facilities, 1994″, in the Federal Register (59 FR 54242) and MMWR (Volume 43, No. RR-13) on October 28, 1994.
All nine classes of air-purifying, particulate respirators to be certified under the provisions of the new particulate filter tests exceed the performance recommendations contained in the CDC Guidelines. Several of these new classes of air-purifying, particulate respirators are expected to be less expensive than respirators with HEPA filters.
Training and Information Requirements
Training shall be provided prior to requiring the employee to wear a respirator in the workplace, and annually thereafter.
Training of temporary or contracted employees is a joint responsibility of the employer and UTHSC. UTHSC must inform the contractor of specific hazards. The employer must provide
training pertaining to the use and maintenance of respiratory protective equipment in accordance with regulatory requirements.
Training in the use of tight-fitting respirators will be performed by or coordinated through Campus Safety, Research Safety, or Occupational Health. Training in the use of N95s or PAPRs used for airborne isolation is the responsibility of the supervising department.
Before any employee wears a respirator for the first time, and annually as long as respirator use is required, they must receive and understand training that covers the following:
- Nature, extent, and effects of respiratory hazards to which the employee may be exposed;
- Explanation of the operation, limitations, and capabilities of the selected respirator(s);
- Instruction in procedures for inspection, donning and removal, checking the fit and seals, and in the wearing of the respirator, including sufficient practice to enable the employee to become thoroughly familiar and confident with the use of the respirator;
- Explanation of the procedures for maintenance and storage;
- How improper fit, use, or maintenance can compromise the protective effect of the respirator
- How to recognize medical signs and symptoms that may limit or prevent effective use of the respirator and reasons to seek repeat medical evaluation from Occupational health.
- Instruction on how to deal with emergency situations involving the use of respirators or with respirator malfunctions; and
- The contents of the OSHA Standard (29 CFR 1910.134), and of the written Respiratory Protection Program, its location and availability.
Responsible Official & Additional Contacts
Subject Matter |
Office Name |
Telephone Number (xxx) xxx-xxxx |
Email/Web Address |
Policy Clarification and Interpretation |
Campus Safety and Emergency Management |
901-448-6114 | |
Policy Training |
Campus Safety and Emergency Management |
901-448-6114 | |
Respiratory Protection Policy |
Campus Safety and Emergency Management |
901-448-6114 |
Related Policies/Guidance Documents
Attachments:
- Appendix A: Voluntary Use Respirator Information
- Appendix B: OSHA Respirator Medical Evaluation Questionnaire
Associated Standards:
- 29 CFR 1910.134 (OSHA), Respiratory Protection
- 42 CFR Part 84 Respiratory Protective Devices
Appendix A
Voluntary Use Respirator Information
Some UTHSC employees and students may choose to use filtering face piece respirators, also referred to as N95 or N99 disposable dust masks, on a voluntary basis during activities that involve exposures to low-level, non- hazardous nuisance dust or other similar particulate. According to the Occupational Safety and Health Administration (OSHA) regulations, UTHSC must provide you with the following information if you wear a filtering face piece respirator voluntarily. The following information is copied from the OSHA Respiratory Protection Standard and pertains to the voluntary use of respirators. After reading the information below, please complete the section at the end of this form.
29 CFR 1910.134, Appendix D – (Mandatory) Information for Employees Using Respirators When Not Required Under the Standard
Respirators are an effective method of protection against designated hazards when properly selected and worn. Respirator use is encouraged, even when exposures are below the exposure limit, to provide an additional level of comfort and protection for workers. However, if a respirator is used improperly or not kept clean, the respirator itself can become a hazard to the worker. Sometimes, workers may wear respirators to avoid exposures to hazards, even if the amount of hazardous substance does not exceed the limits set by OSHA standards. If your employer provides respirators for your voluntary use, or if you provide your own respirator, you need to take certain precautions to be sure that the respirator itself does not present a hazard.
You should do the following:
- Read and heed all instructions provided by the manufacturer on use, maintenance, cleaning and care, and warnings regarding the respirators limitations.
- Choose respirators certified for use to protect against the contaminant of concern. NIOSH, the National Institute for Occupational Safety and Health of the U.S. Department of Health and Human Services, certifies respirators. A label or statement of certification should appear on the respirator or respirator packaging. It will tell you what the respirator is designed for and how much it will protect you.
- Do not wear your respirator into atmospheres containing contaminants for which your respirator is not designed to protect against. For example, a respirator designed to filter dust particles will not protect you against gases, vapors, or very small solid particles of fumes or smoke.
The filtering face piece respirator you have elected to use is approved, when fitted properly, for use against nuisance non-hazardous particulate (e.g., fiberglass, sheet rock dust, sawdust, dirt, pollen, animal dander). It will not provide protection from any chemical vapors such as those associated with spray paints or solvents. It is not intended for use during work that may involve exposure to airborne asbestos fibers, silica dust, or lead dust. Work you perform that may involve airborne asbestos fibers, silica dust, or lead dust should be reviewed by Campus Safety/Occupational Health before the project proceeds. If you have questions concerning any of this information, please contact:
OCCUPATIONAL HEALTH – 901-448-5630
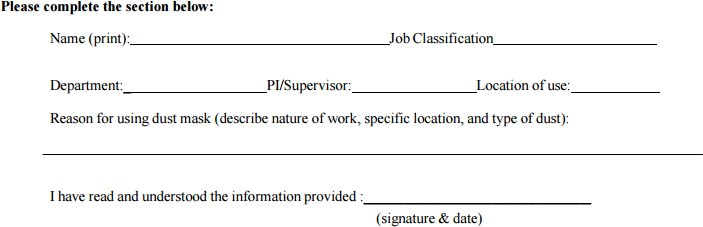
Appendix B
OSHA Respirator Medical Evaluation Questionnaire
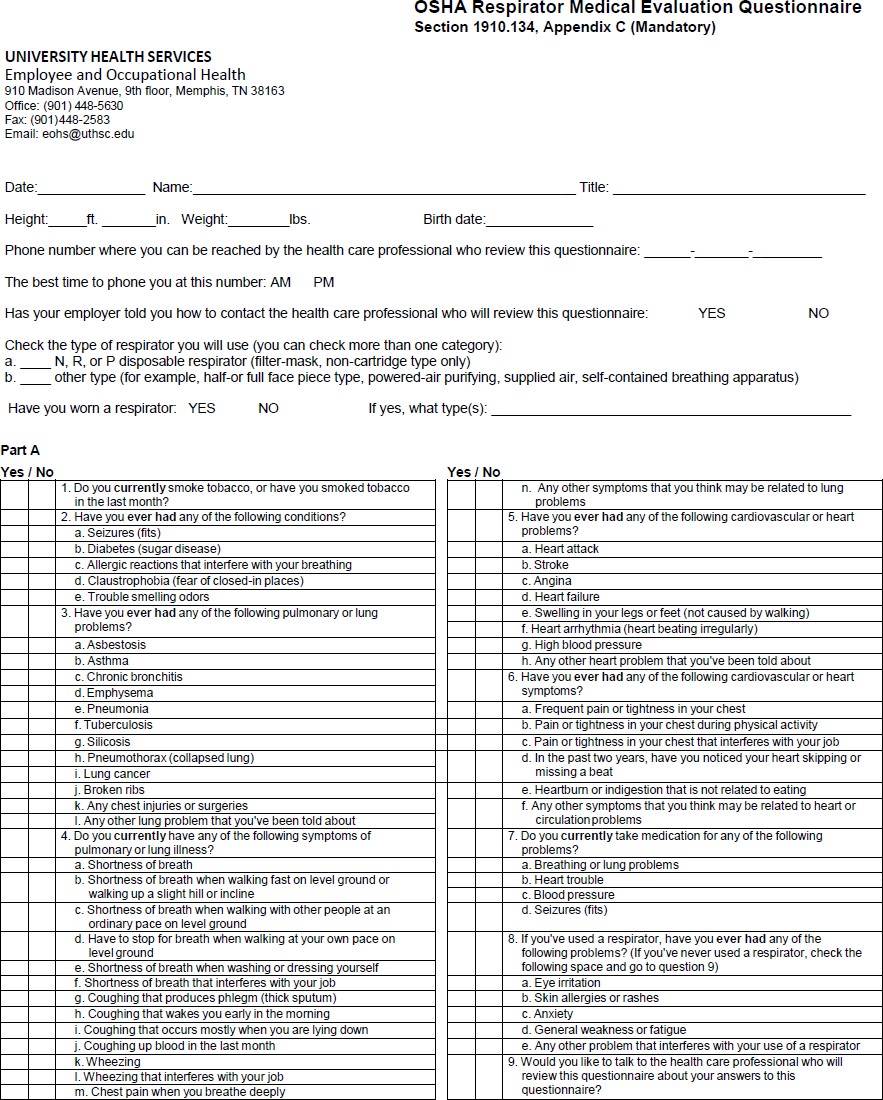
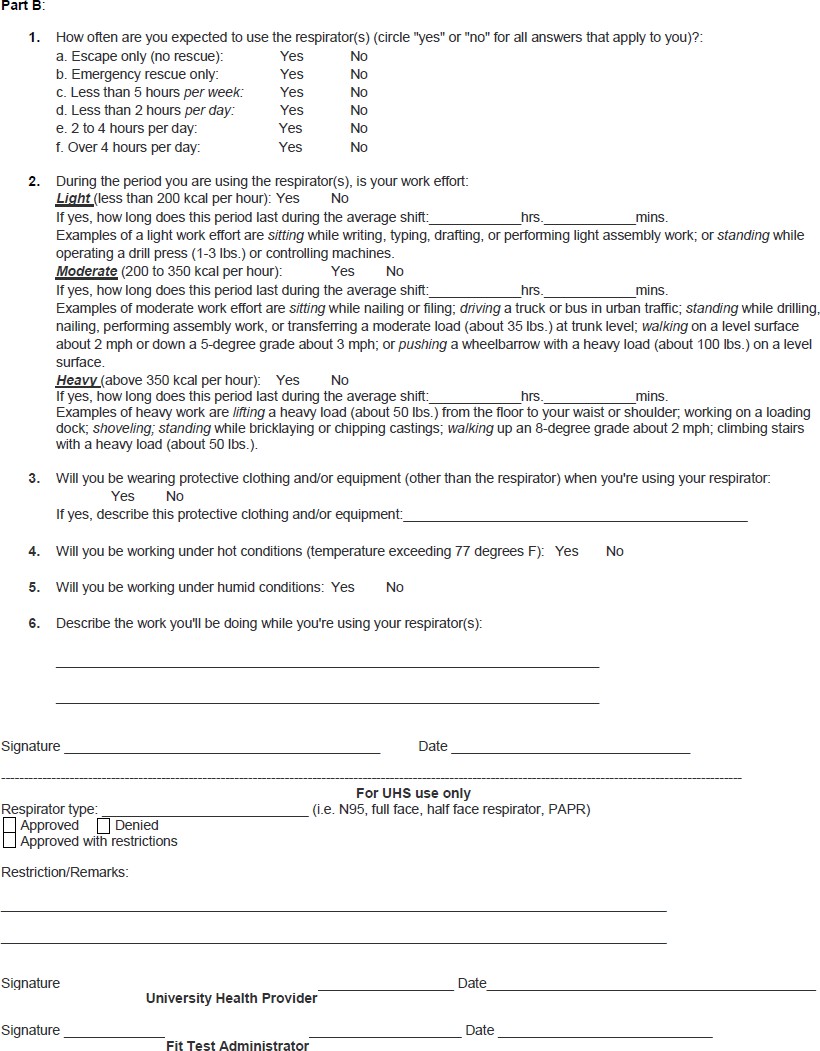
GS5105 – Respiratory Safety Protection Policy
Version: 2 // Effective: 12/19/2023
Downloadable PDF
Related Forms:
GS5105 – Appendix A – Voluntary Use Respirator Information
GS5105 – Appendix B – OSHA Respirator Medical Evaluation Questionnaire