UT Health Science Center GS5115 – Emergency Eyewash and Safety Showers | |
Version: 2 |
Effective Date: 11/20/2023 |
Objective
It shall be the policy of the University of Tennessee health Science Center to provide safety showers and/or eyewash stations in areas where there is a possibility of splash to the body or eyes of acids, caustics, chemicals or pathogens that are injurious to the eyes or present a skin absorption or burn hazard. Safety showers and eyewash stations shall be inspected/tested and shall receive scheduled maintenance.
Scope
These guidelines apply to laboratories (academic and research) and non-laboratory areas such as (but not limited to) maintenance areas and shops at the UTHSC Memphis campus.
Roles
Work Area Supervisors:
- Request installation of emergency eyewash and shower equipment when necessary.
- Ensure unobstructed access to the safety shower/eyewash equipment so that it requires no more than 10 seconds to reach (no more than 55 feet walking distance).
- Ensure that all employees and students who may need the emergency eyewash and shower equipment are trained on their location and use.
- Ensure that emergency eyewash stations within the laboratory are activated weekly and a weekly activation log is maintained.
- Ensure that eyewash stations in their work areas are maintained in a clean and operational state.
- Request maintenance for immediate repair, modification or installation of eyewash/shower equipment.
- Inform Campus Safety before removing any emergency eyewash/shower equipment from the laboratory.
Campus Safety:
- Provide guidance to work areas supervisors in identifying work areas where emergency eyewash units or safety showers are required.
- Recommend appropriate eyewash or shower equipment.
- Coordinate with Facilities Services for inspection, modification, repair, maintenance, and installation of emergency shower and eyewash units, as necessary.
- Assist with building plan review and selection from a list of recommended units during new construction or major renovation.
- Assist with the establishment of testing requirements and procedures to ensure compliance with applicable standards.
Facilities Services:
- Perform immediate modifications, repair, maintenance, and installation of emergency eyewash and shower equipment as required.
- Execute all work orders for the installation or repair of emergency eyewash and shower equipment on a high priority basis.
- Conduct annual preventative maintenance including flow rate, spray pattern testing, and compliance assessments.
- Maintain written records of flow rate testing and compliance assessment.
- Notify Campus Safety of changes in work areas or work processes and practices to evaluate the need for new installations, or for the removal of existing emergency eyewashes or showers.
- Test all emergency equipment after installation to ensure that it meets the manufacturer’s installation requirements. Units that fail testing must be repaired immediately. If deficiencies cannot be immediately corrected for units in a research lab, the work area supervisor or principal investigator (PI) must be notified and the unit must be tagged “DO NOT USE”. Or if the unit is located in the hallway then Facility personnel must tag the unit “DO NOT USE”. The work area supervisor or PI must notify all affected employees in the laboratory and the Facility personnel, when emergency equipment is out of service. A portable unit may be temporarily required to meet the need for an emergency eyewash and shower.
Staff:
- Personnel must know the location of eyewash stations and safety showers available to them in their work area(s).
- Personnel must be aware of first aid procedures requiring the use of eyewash stations and safety showers.
- Personnel must know how to activate eyewash stations and safety showers.
Abbreviations and Definitions
Abbreviations
ANSI: American National Standard Institute
GPM: Gallons per minute
OSHA: Occupational Safety and Health Administration
Definitions
Combination Unit: An interconnected assembly of drenching and flushing equipment that is supplied by a single flushing fluid source.
Drench Hose: A supplemental device consisting of a flexible hose connected to a flushing fluid supply that is used to provide fluid to irrigate face and body areas.
Emergency Eyewash: A device used to provide fluid to irrigate and flush both eyes simultaneously at a velocity low enough to be non-injurious to the user.
Emergency Shower: A device designed to deliver flushing fluid in sufficient volume in order to enable the user to have water cascading over the entire body while the hands are free.
Eye/Face Wash: A device used to provide fluid to irrigate and flush both the face and the eyes simultaneously.
Flushing fluid: Potable water, preserved water, preserved buffered saline solution or other medically acceptable solutions manufactured and labeled in accordance with applicable federal regulations.
Flow Pressure: The pressure of the flushing fluid exerted in the wall of the pipe near the outlet while the faucet/outlet is fully open and flowing.
Flow Regulator: A mechanical device intended to control the flow of flushing fluid through the pipe.
Hazardous Material: Any substance or compound that has the capability of producing adverse effects on human health and safety.
Personal Eyewash: A supplementary device that supports plumbed or self-contained eyewash units, by delivering immediate flushing fluid to the eyes or body.
Plumbed Eyewash: An eyewash unit that is permanently connected to a source of potable water in order to irrigate both eyes
Potable water: Water that is suitable for drinking
Stay-open valve: A valve that, once activated, must be closed manually by the user.
Tepid: Moderately warm; lukewarm
Procedure
Emergency eyewashes, showers, drench hoses and combination units are not substitutes for proper primary protective devices. As a defense against flying solid particles and splashing injurious liquids, workers must wear personal protective equipment as needed, including eye protection, face protection and protective clothing.
The first seconds following an incident involving the eyes are often most critical to keeping injury to a minimum. A personal eyewash may be kept in the immediate vicinity of employees working in a potentially hazardous area. The main purpose of these units is to supply liquid of sufficient quality and quantity for immediate flushing.
Note: A personal eyewash is not a substitute for a code compliant eyewash station. Individuals who first choose to use a personal eyewash should then proceed to a plumbed or self-contained eyewash and flush the eyes for the required minimum 15-minute period.
- General Installation
- Safety showers and eyewashes shall be installed and maintained in compliance with applicable engineering standards and shall be supplied from potable water.
- Pipelines and other parts of safety showers and eyewash stations shall not be used as supports for other types of equipment or fixtures.
- The access routes to safety showers and eyewash stations shall not be blocked. The location of safety showers and eyewash stations may need to be identified with signs that are prominently displayed for immediate recognition if the location is not evident.
- Safety showers and eyewash stations shall be in accessible locations that require no more than 10 seconds for the exposed person to reach along an unobstructed pathway (i.e., no doors which don’t swing open when pushed.
- No obstructions, protrusions, or sharp objects shall be located within 16 inches from the center of the spray pattern of the emergency shower facility.
- Electrical apparatus, telephones, thermostats, or power outlets should not be located within 18 inches of either side of the emergency shower or emergency eyewash facility (i.e., a 36-inch clearance zone).
- Provisions should be made for wastewater disposal for new installations.
- Maintenance
- Eyewash stations shall be maintained Fixed eyewash stations shall be activated weekly to flush the line for a period long enough to verify operation and ensure that flushing fluid is available. This involves opening flow through the nozzles to verify that sufficient fluid is available to neutralize and wash away any corrosive material from a user. In addition, the eyewash fluid should be checked for debris and foreign objects that might cause injury to the eyes. This weekly testing must be documented and should be performed by the department that controls the eyewash.
- Maintain eyewash stations in a manner that is sufficiently clean so as to be free of significant accumulations of dust or other debris.
- An eyewash test log shall be kept near the eyewash. Appendix A is a test log that can be used to document the weekly test. For portable units the duration of flushing will be dependent upon the specified maintenance criteria.
- Personal eyewash units shall be replaced upon expiration of the container.
- Safety showers shall be activated annually by Facilities Services to flush the line and verify proper operation. Documentation of this activity shall be documented on a tag attached to the shower.
- It is the department’s responsibility to ensure that emergency eyewash and safety shower equipment that does not pass inspection is repaired immediately by contacting Facilities
- Whenever an emergency eyewash or safety shower is non-functional, immediately contact Facilities Services to make repairs. Do not handle hazardous materials in that work-area until the unit is returned to proper service.
- Any party removing emergency eyewash or safety shower equipment from service, must notify the affected department beforehand.
- Individuals who may be exposed to hazardous materials shall be instructed in the location and proper use of emergency eyewash and safety shower equipment.
- Portable Eyewash Stations
- Self-contained (portable) eyewash stations are used only as a temporary measure or in areas where it is not feasible to install a fixed eyewash station. The water in these units shall be changed as recommended by the manufacturer. The unit must be capable of delivering a minimum of 1.5 liters per minute (0.4 gpm) and that the flushing fluid covers the areas between the interior and exterior lines of the gauge at some point less than 20.3 cm (8 in.) above the eyewash nozzle(s)
Specifications
The recommended standard for equipment and installation of safety showers, eye/face and drench hoses is identified below in the References section.
- Plumbed Safety Showers
- Heads shall be positioned no less than 82” from floor and no more than 96” from the floor and have a spray pattern with a minimum diameter of 20” at 60” above the floor.
- The flow rate shall be at least 20 gallons per minute (GPM) at a velocity low enough to be non-injurious to the user. The center of spray pattern shall be located at least 16” from any obstruction.
- The valve shall activate in one second or less, have a stay-on feature and stay on until manual reset.
- The handle should be placed a maximum of 69” from the standing surface.
- The valve should be simple to operate and shall go from “off” to “on” in one second or less.
- Eyewash Stations:
- An eye wash unit permanently connected to a source of potable water.
- Heads must be protected from airborne contaminants and positioned six inches from the wall or nearest obstruction.
- The flow rate shall be at least 0.4 gpm for 15 minutes for plumbed units with the valve activating in one second or less.
- The unit shall have a stay-open valve (leaving hands free) feature.
- Eye/Face Wash:
- A device used to irrigate and flush both the face and eyes.
- Heads shall be positioned 33” to 45” from the floor and no closer than six inches from the wall or nearest obstruction.
- Large heads to cover both eyes and face or regular size eyewash heads plus a face spray ring.
- Flow rate should not be less than 0.4 GPM for 15 minutes. The valve shall activate in one second or less and shall have a stay-open valve (leaving hands free) feature. Drench Hoses: A flexible hose connected to a water supply and used to irrigate and flush eyes, face and body areas.
- Hand-held drench hoses support shower and eyewash units but shall not replace them.
- Heads shall have a flow rate of at least 0.4 gpm for 15 minutes. The valve shall activate in one second or less.
Note that the water temperature should not exceed 100 degrees F and should not be lower than 60 degrees F.
Training
- All employees working with hazardous chemicals/materials who may have to use an eyewash or a safety shower shall be trained in the use of the equipment before handling hazardous materials necessitating the availability of such safety equipment.
- Employees should also be made aware of the location of eyewash stations and safety showers before working with hazardous materials in their work areas.
- This information may be included in the department-specific Hazard Communication training or in the laboratory’s chemical hygiene plan.
Responsible Official & Additional Contacts
Subject Matter |
Office Name |
Telephone Number (xxx) xxx-xxxx |
Email/Web Address |
Policy Clarification and Interpretation |
Campus Safety and Emergency Management |
901-448-6114 | |
Policy Training |
Campus Safety and Emergency Management |
901-448-6114 | |
Emergency Eyewash and Safety Showers |
Related Policies/Guidance Documents
Forms Attached
- Emergency Eyewash Weekly Inspection Log
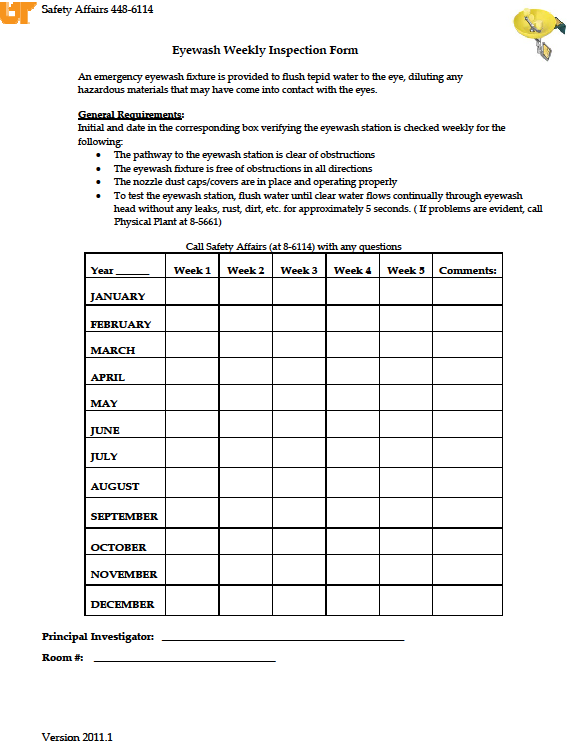